In managerial accounting and business operations, calculating direct labor cost is a critical process for understanding the true cost of production. Accurate calculation of direct labor costs enables businesses to price their products effectively, manage budgets, and improve profitability. In this blog, we will delve into the definition of direct labor, how to calculate it, provide examples, and offer tips on how to reduce these costs. We’ll be discussing:
- What is Direct Labor?
- How to Calculate Direct Labor Cost
- Examples of Direct Labor Cost Calculation
- Tips for Lowering Direct Labor Cost
What is Direct Labor?
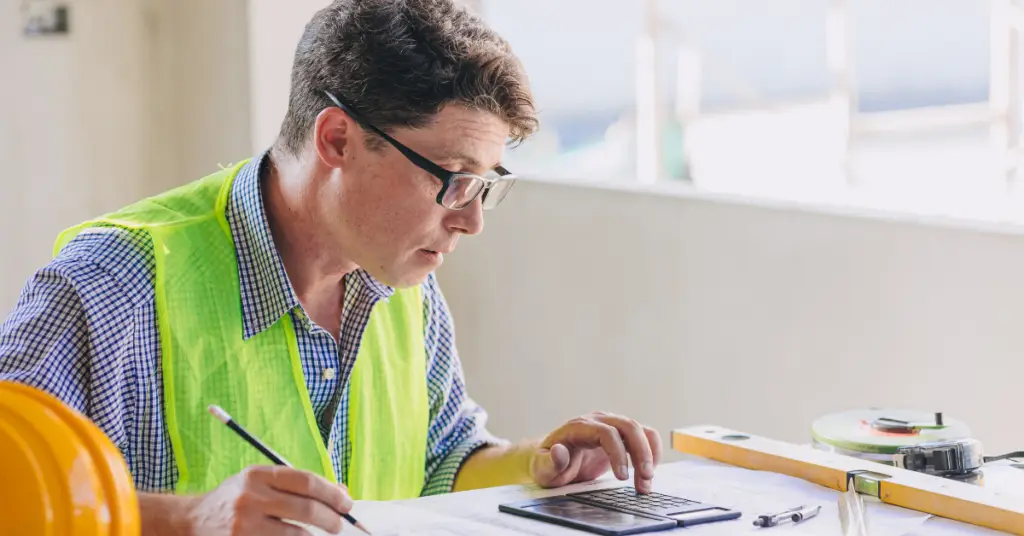
Direct labor is the cost associated with the labor directly involved in the production of goods or services. This includes wages, salaries, and benefits for employees who work directly on the manufacturing line, in the assembly process, or in any role where their work is directly tied to the creation of a product or service.
For example, in a manufacturing company, direct labor would include the wages paid to workers who assemble products on the production line. In a service-oriented business, such as a catering company, direct labor costs would include the wages paid to chefs and servers who prepare and deliver the food.
Direct labor is an essential component of cost accounting because it directly impacts the cost of goods sold (COGS). It’s also a variable cost, meaning it fluctuates with the level of production or service delivery. The more products or services you produce, the higher your direct labor costs will be.
How to Calculate Direct Labor Cost
Calculating direct labor costs involves several steps and requires careful consideration of all the components involved.
1. Identify the Number of Direct Labor Hours
This includes the time spent by employees who are directly involved in production. To find this, multiply the number of employees by the number of hours they work.
Total Direct Labor Hours = Number of Workers × Hours Worked Per Week
2. Determine the Hourly Wage Rate
This rate includes not only their base salary but also additional costs such as payroll taxes, benefits, and any overtime pay.
Total Hourly Wage Rate = Base Wage Rate + Additional Costs
3. Calculate the Total Direct Labor Cost
Once you have the total direct labor hours and the total hourly wage rate, multiply them to calculate the total direct labor cost.
Total Direct Labor Cost = Total Direct Labor Hours × Total Hourly Wage Rate
Examples of Direct Labor Cost Calculation
To further illustrate how to calculate direct labor costs, let’s consider a few examples.
Example 1: Manufacturing Company
Imagine a furniture manufacturing company where workers are paid $18 per hour, plus $7 in additional costs (including benefits and taxes). The company has 15 workers, each working 35 hours per week.
- Total Direct Labor Hours = 15 workers × 35 hours/week = 525 hours/week
- Total Hourly Wage Rate = $18/hour + $7/hour = $25/hour
- Total Direct Labor Cost = 525 hours/week × $25/hour = $13,125/week
In this example, the weekly direct labor cost for the furniture company is $13,125.
Related Read: Inventory Management for Manufacturers: Comprehensive Guide
Example 2: Service-Based Business
Consider a cleaning service company with employees earning $15 per hour, plus an additional $3 for benefits. The company employs 8 cleaners, each working 30 hours a week.
- Total Direct Labor Hours = 8 cleaners × 30 hours/week = 240 hours/week
- Total Hourly Wage Rate = $15/hour + $3/hour = $18/hour
- Total Direct Labor Cost = 240 hours/week × $18/hour = $4,320/week
Here, the weekly direct labor cost for the cleaning service company is $4,320.
Tips for Lowering Direct Labor Cost
While direct labor costs are a necessary part of running a business, there are strategies you can implement to reduce these costs without compromising quality or productivity.
1. Invest in Employee Training
Investing in employee training can improve efficiency and reduce errors, leading to fewer hours needed to complete tasks. Well-trained employees are more productive, and their work is of higher quality, reducing the need for rework and the associated labor costs.
2. Implement Lean Manufacturing Practices
Lean manufacturing principles focus on reducing waste and improving processes. By streamlining production processes, businesses can reduce the amount of labor required to produce goods, which in turn lowers direct labor costs.
3. Optimize Scheduling
Effective scheduling ensures that employees are working at times when they are most needed, reducing idle time and minimizing overtime costs. By matching labor supply with demand more closely, businesses can reduce unnecessary labor expenses.
4. Automate Where Possible
Automation can significantly reduce the amount of direct labor required. Investing in technology to automate repetitive tasks can reduce the need for manual labor, leading to lower direct labor costs over time.
5. Outsource Non-Core Activities
Outsourcing tasks that are not core to your business can be a cost-effective way to reduce direct labor costs. For example, outsourcing payroll, IT services, or other administrative tasks allows you to focus your labor resources on areas that directly contribute to production.
Conclusion
Understanding and calculating direct labor costs is essential for accurate pricing, budgeting, and overall financial management in any business. By carefully calculating direct labor hours, considering all wage-related expenses, and implementing strategies to reduce these costs, businesses can improve their profitability and maintain a competitive edge.
For an even more streamlined approach, consider using Vencru’s all-in-one business management software. Vencru simplifies cost tracking and financial reporting, helping you gain better control over your expenses and boost profitability.
Related Content