Kitting involves grouping individual components or products together to create a single package, or “kit,” in manufacturing and warehousing. This kit then functions as a single item for inventory management, production, or shipment. Industries frequently use kitting when multiple components are necessary to assemble a final product. By pre-assembling these components into kits, businesses can streamline their operations, reduce handling time, and improve efficiency.
In a warehouse, workers gather all the necessary parts and package them together before sending them to the production line or directly to the customer. This process helps in simplifying the supply chain, ensuring that all required components are readily available when needed.
What Is Inventory Kitting?
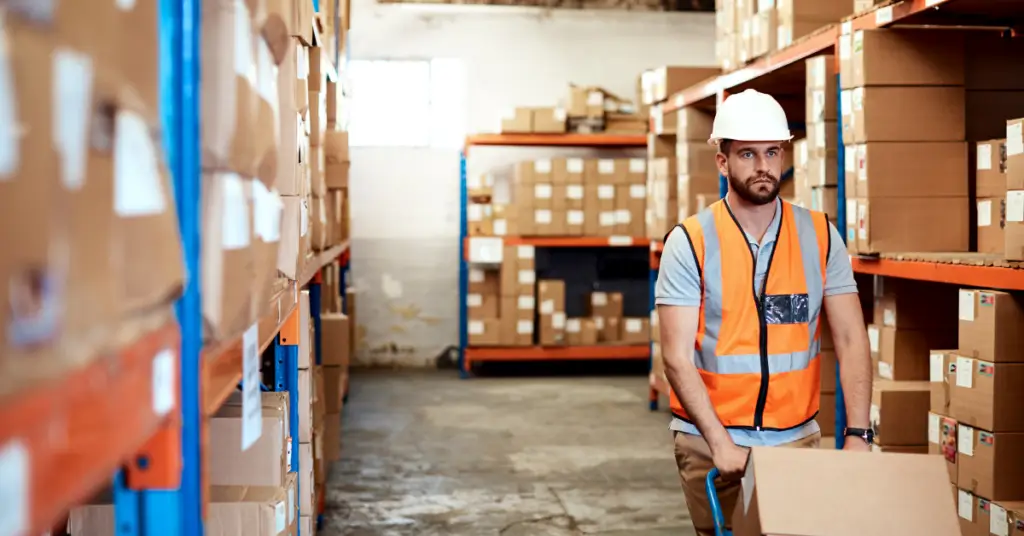
Inventory kitting refers to the management and organization of kits within a warehouse or manufacturing environment. Instead of tracking each component individually, inventory kitting allows businesses to manage the kit as a single inventory item. This can simplify inventory control, as it reduces the complexity of managing multiple parts separately.
In practice, inventory kitting involves creating a bill of materials (BOM) that lists all the components required to assemble the kit. Once the team creates the kit, they assign it a unique SKU (Stock Keeping Unit) and track it as a single entity. This approach not only improves inventory accuracy but also speeds up the picking and packing process, as warehouse staff only need to locate and handle one item instead of multiple parts.
Why Is Kitting Important?
Kitting is important because it streamlines operations, reduces errors, and enhances productivity. By pre-assembling kits, companies can ensure that all necessary components are available in one place, reducing the time spent searching for individual parts. This is particularly beneficial in manufacturing environments where time is of the essence, and any delay can disrupt the production process.
Moreover, kitting helps in reducing the risk of errors. When staff pick components individually, mistakes, such as selecting the wrong part or missing a component, are more likely. Kitting reduces this risk by consolidating all the necessary items into a single kit, which they can verify before using it in production or shipping it to the customer.
Benefits of Kitting
Kitting offers several benefits that can significantly impact the efficiency and effectiveness of manufacturing and warehousing operations.
- Improved Efficiency: Kitting reduces the time spent on picking and packing because staff pre-assemble all components into a single package. This leads to faster production cycles and quicker order fulfillment.
- Cost Savings: By streamlining the picking process, kitting can reduce labor costs. Additionally, it minimizes the risk of errors, which can lead to cost savings by avoiding rework or returns.
- Better Inventory Management: With kitting, inventory management becomes more straightforward. Instead of tracking multiple components, businesses can manage a single SKU for each kit, simplifying inventory control and reducing the chances of stockouts or overstocking.
- Enhanced Customer Satisfaction: Kitting ensures that customers receive complete and accurate orders, leading to higher customer satisfaction. It also allows for faster shipping times, which is a key factor in customer loyalty.
Private Kitting
Private kitting refers to the process of creating custom kits tailored to the specific needs of a customer. This is often used in industries where customers require a unique combination of components that are not typically offered together. For example, in the electronics industry, a customer might need a specific set of components for a custom-built device. Private kitting allows the business to assemble these components into a single kit, making it easier for the customer to receive exactly what they need.
Private kitting can also be used for promotional purposes, where businesses create special kits that bundle complementary products together at a discounted price. This not only enhances the customer experience but also helps in clearing out excess inventory.
How to Manage Kitting
Managing kitting effectively requires careful planning and coordination. Here are some key steps to manage kitting in a warehouse or manufacturing environment:
- Create a Bill of Materials (BOM): The first step in managing kitting is to create a BOM that lists all the components required for the kit. This document serves as a blueprint for assembling the kit and ensures that nothing is missed.
- Assign a Unique SKU: Once the kit is assembled, assign a unique SKU to it. This makes it easier to track the kit in the inventory system and simplifies the picking and packing process.
- Automate the Kitting Process: Wherever possible, automate the kitting process to reduce manual labor and minimize the risk of errors. This can include using conveyor belts, automated picking systems, and barcode scanners.
- Regularly Review and Update Kits: As customer needs and product offerings change, regularly review and update the kits to ensure they remain relevant and cost-effective.
- Train Staff on Kitting Procedures: Ensure that all staff involved in the kitting process are well-trained and understand the importance of accuracy and efficiency. Regular training sessions can help in maintaining high standards and reducing errors.
Kitting in Manufacturing
In manufacturing, kitting plays a crucial role in ensuring that production lines run smoothly. By pre-assembling kits with all the necessary components, manufacturers can reduce downtime and ensure that production schedules are met.
Kitting is particularly important in lean manufacturing environments, where minimizing waste and maximizing efficiency are key priorities. By reducing the time spent on searching for and handling individual components, kitting helps in keeping the production line moving and reduces the risk of bottlenecks.
In addition to improving efficiency, kitting can also enhance quality control in manufacturing. Consolidating components into kits allows manufacturers to perform quality checks before using the kit in production, ensuring all parts meet the required standards.
Implement Kitting With Inventory Management Software
To fully leverage the benefits of kitting, it is essential to implement inventory management software that supports kitting functionality. This software can automate many aspects of the kitting process, from creating BOMs to tracking kits in the inventory system.
Inventory management software can also provide real-time visibility into stock levels, making it easier to manage kitting operations and avoid stockouts. Additionally, it can integrate with other systems, such as ERP (Enterprise Resource Planning) and CRM (Customer Relationship Management) software, to provide a seamless flow of information across the organization.
By using inventory management software, businesses can optimize their kitting operations, improve accuracy, and reduce the time spent on manual tasks. This not only enhances efficiency but also provides a better experience for customers, who can expect faster and more accurate deliveries.
Conclusion
Kitting is a powerful tool for improving efficiency, reducing costs, and enhancing customer satisfaction in both manufacturing and warehousing environments. By understanding what kitting is, how it works, and the benefits it offers, businesses can streamline their operations and gain a competitive edge.
Whether it’s through inventory kitting, private kitting, or using inventory management software, implementing kitting strategies can lead to significant improvements in productivity and profitability. As the business landscape continues to evolve, kitting will remain an essential component of successful supply chain management.
Related Content